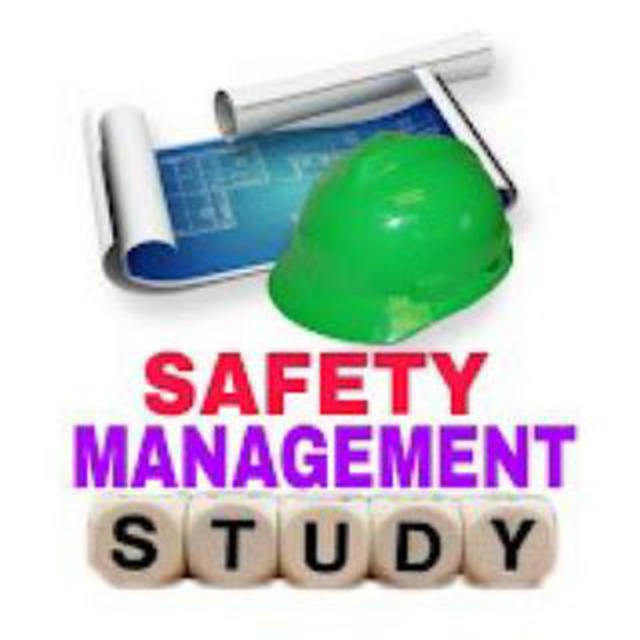
Safety Mgmt Study
Welcome to Safety Management Study! Join our Telegram channel for the latest information, tips, and updates on safety officer roles, Health, Safety, and Environment (HSE) practices, job opportunities, and safety videos. Stay informed and enhance your safe
Recent Posts
Q.4
1. Chemical Safety Data Sheets (SDS) Accessibility
Ensure that chemical safety data sheets (SDS) are readily accessible to workers.
The chemicals used in the paint production process must be handled safely, and SDS contain vital information about their properties, hazards, and safe handling procedures.
Having SDS readily available helps workers understand the risks associated with the chemicals they handle and follow the correct safety procedures to prevent accidents.
2. Regular Safety Inspections and Audits
Conduct regular safety inspections and audits of chemical storage and handling areas.
The introduction of bulk storage tanks for raw materials requires frequent checks to ensure everything is functioning as expected and complies with safety standards.
Safety inspections help identify potential hazards and weaknesses in the system, allowing corrective actions to be taken before an incident occurs.
3. Standard Operating Procedures (SOPs) for Chemical Handling
Develop and implement clear standard operating procedures (SOPs) for the handling of chemicals.
The project has introduced bulk storage systems and pumping equipment for handling chemicals, which should be governed by written SOPs outlining safe handling, storage, and emergency response measures.
SOPs ensure that workers follow consistent and safe practices when handling chemicals, reducing the risk of human error and accidents.
4. Permit to Work System
Introduce a permit to work system for highrisk activities involving chemicals.
Certain tasks, such as cleaning tanks or maintaining the bulk storage systems, may pose a significant risk due to chemical exposure.
A permit to work system ensures that these tasks are carried out only when appropriate safety measures are in place, reducing the likelihood of accidents.
5. Routine Maintenance and Equipment Checks
Establish routine maintenance schedules for chemical storage and handling equipment.
The new pumping and piping systems used for bulk chemical transfer require regular checks to ensure they are in good working order and do not pose a risk of leaks or malfunctions.
Regular equipment maintenance ensures that any faults are identified and corrected before they lead to incidents, preventing spills, leaks, or system failures.
6. Emergency Response Plans
Implement detailed emergency response plans for chemical spills and leaks.
Given the increased volume and hazard level of chemicals in bulk storage, having a clear, practiced response plan is critical.
Emergency response plans guide workers on how to act in case of an accident, reducing the severity of incidents by ensuring prompt and effective action to contain the hazard.
7. Clear Labeling and Signage
Ensure that all chemicals and chemical storage areas are clearly labeled with appropriate hazard symbols and handling instructions.
Bulk chemicals in storage tanks and transfer lines need to be easily identifiable, so workers know what they’re handling at all times.
Clear labeling and signage reduce the risk of mishandling chemicals, ensuring that workers follow the right procedures based on the material's specific hazards.
8. Worker Training and Refresher Courses
Provide regular training and refresher courses for all workers handling chemicals.
Following the changes introduced by the project, such as bulk chemical handling, workers need to be trained on the new systems and best practices.
Continuous training ensures that workers stay informed of updated safety protocols and are competent in handling chemicals safely, reducing the likelihood of incidents due to human error.
1. Chemical Safety Data Sheets (SDS) Accessibility
Ensure that chemical safety data sheets (SDS) are readily accessible to workers.
The chemicals used in the paint production process must be handled safely, and SDS contain vital information about their properties, hazards, and safe handling procedures.
Having SDS readily available helps workers understand the risks associated with the chemicals they handle and follow the correct safety procedures to prevent accidents.
2. Regular Safety Inspections and Audits
Conduct regular safety inspections and audits of chemical storage and handling areas.
The introduction of bulk storage tanks for raw materials requires frequent checks to ensure everything is functioning as expected and complies with safety standards.
Safety inspections help identify potential hazards and weaknesses in the system, allowing corrective actions to be taken before an incident occurs.
3. Standard Operating Procedures (SOPs) for Chemical Handling
Develop and implement clear standard operating procedures (SOPs) for the handling of chemicals.
The project has introduced bulk storage systems and pumping equipment for handling chemicals, which should be governed by written SOPs outlining safe handling, storage, and emergency response measures.
SOPs ensure that workers follow consistent and safe practices when handling chemicals, reducing the risk of human error and accidents.
4. Permit to Work System
Introduce a permit to work system for highrisk activities involving chemicals.
Certain tasks, such as cleaning tanks or maintaining the bulk storage systems, may pose a significant risk due to chemical exposure.
A permit to work system ensures that these tasks are carried out only when appropriate safety measures are in place, reducing the likelihood of accidents.
5. Routine Maintenance and Equipment Checks
Establish routine maintenance schedules for chemical storage and handling equipment.
The new pumping and piping systems used for bulk chemical transfer require regular checks to ensure they are in good working order and do not pose a risk of leaks or malfunctions.
Regular equipment maintenance ensures that any faults are identified and corrected before they lead to incidents, preventing spills, leaks, or system failures.
6. Emergency Response Plans
Implement detailed emergency response plans for chemical spills and leaks.
Given the increased volume and hazard level of chemicals in bulk storage, having a clear, practiced response plan is critical.
Emergency response plans guide workers on how to act in case of an accident, reducing the severity of incidents by ensuring prompt and effective action to contain the hazard.
7. Clear Labeling and Signage
Ensure that all chemicals and chemical storage areas are clearly labeled with appropriate hazard symbols and handling instructions.
Bulk chemicals in storage tanks and transfer lines need to be easily identifiable, so workers know what they’re handling at all times.
Clear labeling and signage reduce the risk of mishandling chemicals, ensuring that workers follow the right procedures based on the material's specific hazards.
8. Worker Training and Refresher Courses
Provide regular training and refresher courses for all workers handling chemicals.
Following the changes introduced by the project, such as bulk chemical handling, workers need to be trained on the new systems and best practices.
Continuous training ensures that workers stay informed of updated safety protocols and are competent in handling chemicals safely, reducing the likelihood of incidents due to human error.
Compliance
It’s important to train workers on relevant health and safety regulations, particularly in light of the project’s changes.
With the new bulk storage and handling systems, the company needs to comply with updated regulatory standards related to chemical handling and workplace safety.
This training ensures workers are aware of their rights and responsibilities under health and safety laws, reducing the likelihood of compliance violations and accidents.
It’s important to train workers on relevant health and safety regulations, particularly in light of the project’s changes.
With the new bulk storage and handling systems, the company needs to comply with updated regulatory standards related to chemical handling and workplace safety.
This training ensures workers are aware of their rights and responsibilities under health and safety laws, reducing the likelihood of compliance violations and accidents.
Q.3
1. Training on Bulk Storage Handling
Workers need training on the proper handling and safety procedures for bulk materials.
The raw materials are now delivered by tanker and pumped into storage tanks, replacing the old method of handling 25litre drums.
Training in bulk storage handling is essential to ensure workers understand how to safely manage larger quantities of raw materials, preventing accidents such as spills or leaks.
2. Training on New Equipment and Machinery
Workers should be trained on the new pumping and pipework systems used for transferring raw materials.
The project introduced new equipment to pump materials directly from tankers into storage tanks.
Ensuring that workers are competent in operating and maintaining new machinery will reduce the risk of mechanical failures, safety incidents, and operational inefficiencies.
3. Hazardous Material Handling and Safety
Workers should receive training on the safe handling of hazardous chemicals, especially in bulk storage.
Raw materials in bulk form can pose additional risks, such as chemical reactions or spills, which were not present when handled in smaller quantities.
Proper hazardous material handling training will equip workers with the knowledge to mitigate the risks associated with these substances and respond appropriately in emergencies.
4. Risk Assessment and Hazard Identification
Training on how to perform risk assessments and identify potential hazards in the new system.
The changes to raw material delivery and storage systems introduced new hazards that must be recognized and controlled.
Risk assessment training ensures that workers can identify hazards in their daily tasks and implement controls to prevent incidents.
5. Emergency Response Training
Workers should be trained in emergency response procedures, particularly for handling chemical spills or leaks.
With bulk raw material handling, there is an increased risk of spills or other emergencies that could require immediate action.
Training in emergency response ensures that workers are prepared to respond quickly and efficiently to mitigate potential harm to the environment or people.
6. Fire Safety
fire safety training, as handling chemicals and large quantities of materials can increase the risk of accidents.
Chemical handling, equipment use, and potential hazards, such as fires or burns, can occur during the new process.
First aid and fire safety training help workers manage immediate health and safety risks until professional help arrives, reducing the severity of injuries.
7. Manual Handling and Ergonomics
Training on safe manual handling techniques should be provided, as the introduction of bulk materials may require more physical effort.
While bulk storage reduces the need for manual drum handling, there are still tasks related to moving equipment or materials that require physical labor.
Proper manual handling training helps prevent musculoskeletal injuries, ensuring workers can perform tasks safely without strain.
8. Work Flow and Process Optimization
Workers should be trained in the updated workflows and processes introduced by the project.
The shift from smaller drum deliveries to bulk storage alters how materials are transferred, handled, and processed within the production line.
Training on the new workflows ensures that workers understand the steps involved in the process, improving overall efficiency and reducing mistakes.
10. Chemical Safety and Personal Protective Equipment (PPE)
Workers should receive detailed training on chemical safety and proper PPE usage.
Handling bulk quantities of chemicals increases exposure risks, requiring appropriate PPE such as gloves, goggles, and aprons.
PPE training ensures workers are properly protected from chemical exposure and other hazards, reducing the likelihood of accidents.
11. Health and Safety Regulations and
1. Training on Bulk Storage Handling
Workers need training on the proper handling and safety procedures for bulk materials.
The raw materials are now delivered by tanker and pumped into storage tanks, replacing the old method of handling 25litre drums.
Training in bulk storage handling is essential to ensure workers understand how to safely manage larger quantities of raw materials, preventing accidents such as spills or leaks.
2. Training on New Equipment and Machinery
Workers should be trained on the new pumping and pipework systems used for transferring raw materials.
The project introduced new equipment to pump materials directly from tankers into storage tanks.
Ensuring that workers are competent in operating and maintaining new machinery will reduce the risk of mechanical failures, safety incidents, and operational inefficiencies.
3. Hazardous Material Handling and Safety
Workers should receive training on the safe handling of hazardous chemicals, especially in bulk storage.
Raw materials in bulk form can pose additional risks, such as chemical reactions or spills, which were not present when handled in smaller quantities.
Proper hazardous material handling training will equip workers with the knowledge to mitigate the risks associated with these substances and respond appropriately in emergencies.
4. Risk Assessment and Hazard Identification
Training on how to perform risk assessments and identify potential hazards in the new system.
The changes to raw material delivery and storage systems introduced new hazards that must be recognized and controlled.
Risk assessment training ensures that workers can identify hazards in their daily tasks and implement controls to prevent incidents.
5. Emergency Response Training
Workers should be trained in emergency response procedures, particularly for handling chemical spills or leaks.
With bulk raw material handling, there is an increased risk of spills or other emergencies that could require immediate action.
Training in emergency response ensures that workers are prepared to respond quickly and efficiently to mitigate potential harm to the environment or people.
6. Fire Safety
fire safety training, as handling chemicals and large quantities of materials can increase the risk of accidents.
Chemical handling, equipment use, and potential hazards, such as fires or burns, can occur during the new process.
First aid and fire safety training help workers manage immediate health and safety risks until professional help arrives, reducing the severity of injuries.
7. Manual Handling and Ergonomics
Training on safe manual handling techniques should be provided, as the introduction of bulk materials may require more physical effort.
While bulk storage reduces the need for manual drum handling, there are still tasks related to moving equipment or materials that require physical labor.
Proper manual handling training helps prevent musculoskeletal injuries, ensuring workers can perform tasks safely without strain.
8. Work Flow and Process Optimization
Workers should be trained in the updated workflows and processes introduced by the project.
The shift from smaller drum deliveries to bulk storage alters how materials are transferred, handled, and processed within the production line.
Training on the new workflows ensures that workers understand the steps involved in the process, improving overall efficiency and reducing mistakes.
10. Chemical Safety and Personal Protective Equipment (PPE)
Workers should receive detailed training on chemical safety and proper PPE usage.
Handling bulk quantities of chemicals increases exposure risks, requiring appropriate PPE such as gloves, goggles, and aprons.
PPE training ensures workers are properly protected from chemical exposure and other hazards, reducing the likelihood of accidents.
11. Health and Safety Regulations and
The new bulk storage system could introduce changes in how waste materials are managed.
The use of tanker deliveries and bulk storage tanks may produce different types or quantities of waste.
Change management would ensure that the waste disposal and management procedures are adjusted to comply with environmental and safety standards.
The use of tanker deliveries and bulk storage tanks may produce different types or quantities of waste.
Change management would ensure that the waste disposal and management procedures are adjusted to comply with environmental and safety standards.
Q.2
1. Change in Raw Material Handling Process
The introduction of bulk delivery and storage of raw materials required a change in the handling process.
The raw materials, previously stored in 25litre drums, were now delivered by tanker and pumped directly into storage tanks.
This significant shift in handling required new safety procedures, training, and equipment to ensure worker safety and maintain operational efficiency.
2. Changes in Storage Facilities
The switch to bulk storage tanks altered the existing storage infrastructure.
New storage tanks were installed to hold raw materials, replacing the previous drum storage method.
A change control process would be necessary to manage the installation of new equipment, ensuring safety and compliance with regulations.
3. Change in Equipment and Machinery
The installation of new equipment for pumping raw materials required careful control.
New pipework and pumping systems were installed to transport materials from the bulk storage tanks to the mixers.
Managing this change ensures that the new systems are safe, comply with health and safety regulations, and are compatible with the existing production process.
4. Modification of Workflows
The shift to bulk delivery and storage impacted production workflows.
The need to change how raw materials are delivered, handled, and transferred to the production area disrupted existing workflows.
Change controls would ensure the new workflows are optimized, and employees are trained on the updated processes.
5. Changes in Risk Assessment
The change in raw material handling and storage required an updated risk assessment.
The introduction of tanker deliveries and bulk storage significantly altered the risk landscape.
A new risk assessment would identify and evaluate new hazards, ensuring that controls are implemented for the safe management of these changes.
6. Update to Health and Safety Procedures
The implementation of bulk storage and transfer processes necessitated updates to health and safety procedures.
Worker safety measures would need to reflect the new methods of handling hazardous materials.
Change controls would ensure that all updated safety procedures are in place and followed throughout the process.
7. Changes in Personnel Training
Training for workers would need to be updated to reflect the new raw material handling processes.
The shift from manual drum handling to tanker deliveries and automated pumping systems would require workers to be retrained.
Management of change ensures that training programs are updated and that employees are equipped to handle new equipment and processes safely.
8. Changes in Accident Reporting and Investigation Procedures
New procedures for accident reporting and investigation might have been required as a result of the process changes.
The introduction of new handling systems and equipment could lead to different accident risks.
Change controls would ensure that reporting and investigation protocols are adapted to identify and address potential new risks.
9. Modification of Emergency Response Plans
Changes in the materials used and the processes employed could require updates to emergency response plans.
Bulk storage of raw materials and pumping systems may introduce new types of emergencies, such as chemical spills or fires.
Change management would ensure that emergency response plans are updated to reflect these new risks and that all staff are trained in the revised procedures.
10. Changes to the Supply Chain
The shift to bulk delivery could require changes in the supply chain logistics.
The need for bulk deliveries by tanker instead of smaller drum shipments affects the supply chain.
Change controls would ensure the new supply chain process is efficient, reliable, and safe for all stakeholders.
11. Modifications to Waste Management Procedures
1. Change in Raw Material Handling Process
The introduction of bulk delivery and storage of raw materials required a change in the handling process.
The raw materials, previously stored in 25litre drums, were now delivered by tanker and pumped directly into storage tanks.
This significant shift in handling required new safety procedures, training, and equipment to ensure worker safety and maintain operational efficiency.
2. Changes in Storage Facilities
The switch to bulk storage tanks altered the existing storage infrastructure.
New storage tanks were installed to hold raw materials, replacing the previous drum storage method.
A change control process would be necessary to manage the installation of new equipment, ensuring safety and compliance with regulations.
3. Change in Equipment and Machinery
The installation of new equipment for pumping raw materials required careful control.
New pipework and pumping systems were installed to transport materials from the bulk storage tanks to the mixers.
Managing this change ensures that the new systems are safe, comply with health and safety regulations, and are compatible with the existing production process.
4. Modification of Workflows
The shift to bulk delivery and storage impacted production workflows.
The need to change how raw materials are delivered, handled, and transferred to the production area disrupted existing workflows.
Change controls would ensure the new workflows are optimized, and employees are trained on the updated processes.
5. Changes in Risk Assessment
The change in raw material handling and storage required an updated risk assessment.
The introduction of tanker deliveries and bulk storage significantly altered the risk landscape.
A new risk assessment would identify and evaluate new hazards, ensuring that controls are implemented for the safe management of these changes.
6. Update to Health and Safety Procedures
The implementation of bulk storage and transfer processes necessitated updates to health and safety procedures.
Worker safety measures would need to reflect the new methods of handling hazardous materials.
Change controls would ensure that all updated safety procedures are in place and followed throughout the process.
7. Changes in Personnel Training
Training for workers would need to be updated to reflect the new raw material handling processes.
The shift from manual drum handling to tanker deliveries and automated pumping systems would require workers to be retrained.
Management of change ensures that training programs are updated and that employees are equipped to handle new equipment and processes safely.
8. Changes in Accident Reporting and Investigation Procedures
New procedures for accident reporting and investigation might have been required as a result of the process changes.
The introduction of new handling systems and equipment could lead to different accident risks.
Change controls would ensure that reporting and investigation protocols are adapted to identify and address potential new risks.
9. Modification of Emergency Response Plans
Changes in the materials used and the processes employed could require updates to emergency response plans.
Bulk storage of raw materials and pumping systems may introduce new types of emergencies, such as chemical spills or fires.
Change management would ensure that emergency response plans are updated to reflect these new risks and that all staff are trained in the revised procedures.
10. Changes to the Supply Chain
The shift to bulk delivery could require changes in the supply chain logistics.
The need for bulk deliveries by tanker instead of smaller drum shipments affects the supply chain.
Change controls would ensure the new supply chain process is efficient, reliable, and safe for all stakeholders.
11. Modifications to Waste Management Procedures
Q.1.b
1. Identifies NonCompliance Issues
Reviewing audit findings helps identify areas where legal or procedural noncompliance exists.
The audit revealed that health and safety documents were outdated by three years.
Regular reviews ensure the organization updates its policies and practices to comply with legal and industry standards.
2. Improves Workplace Safety
Audits highlight hazards and risks that need addressing.
The audit found issues with chemical storage and manual handling.
Reviewing these findings ensures corrective measures are taken, reducing the risk of workplace accidents and health issues.
3. Enhances Worker Engagement and Feedback
Reviewing findings ensures that worker concerns are acknowledged and addressed.
Worker C reported dermatitis and work fatigue during the audit.
Addressing such concerns improves worker morale, trust in management, and overall workplace culture.
4. Drives Continuous Improvement
Reviewing audit findings supports ongoing safety and operational improvements.
The organization decided to switch to bulk storage and transfer of raw materials.
Regularly assessing findings helps businesses refine their processes, making them safer and more efficient.
5. Ensures Accountability for Corrective Actions
Findings review assigns responsibility for implementing safety improvements.
The PM was given two months to resolve chemical storage issues.
Holding individuals accountable ensures corrective actions are completed within a set timeframe.
6. Supports Legal and Regulatory Compliance
Audit reviews help organizations comply with health and safety regulations.
The audit identified noncompliance with chemical handling procedures.
Reviewing and acting on findings ensures that businesses meet regulatory requirements, avoiding legal consequences.
7. Helps in Measuring Safety Performance
Reviewing findings provides key data to assess improvements in health and safety.
Followup audits can compare conditions before and after corrective actions.
Tracking progress helps organizations understand the effectiveness of their safety initiatives and make further improvements.
8. Reduces Financial and Reputational Risks
Addressing audit findings prevents costly incidents and reputational damage.
Poor chemical handling could lead to spills, injuries, or regulatory fines.
Proactive reviews minimize risks, reducing compensation claims, legal penalties, and negative publicity.
1. Identifies NonCompliance Issues
Reviewing audit findings helps identify areas where legal or procedural noncompliance exists.
The audit revealed that health and safety documents were outdated by three years.
Regular reviews ensure the organization updates its policies and practices to comply with legal and industry standards.
2. Improves Workplace Safety
Audits highlight hazards and risks that need addressing.
The audit found issues with chemical storage and manual handling.
Reviewing these findings ensures corrective measures are taken, reducing the risk of workplace accidents and health issues.
3. Enhances Worker Engagement and Feedback
Reviewing findings ensures that worker concerns are acknowledged and addressed.
Worker C reported dermatitis and work fatigue during the audit.
Addressing such concerns improves worker morale, trust in management, and overall workplace culture.
4. Drives Continuous Improvement
Reviewing audit findings supports ongoing safety and operational improvements.
The organization decided to switch to bulk storage and transfer of raw materials.
Regularly assessing findings helps businesses refine their processes, making them safer and more efficient.
5. Ensures Accountability for Corrective Actions
Findings review assigns responsibility for implementing safety improvements.
The PM was given two months to resolve chemical storage issues.
Holding individuals accountable ensures corrective actions are completed within a set timeframe.
6. Supports Legal and Regulatory Compliance
Audit reviews help organizations comply with health and safety regulations.
The audit identified noncompliance with chemical handling procedures.
Reviewing and acting on findings ensures that businesses meet regulatory requirements, avoiding legal consequences.
7. Helps in Measuring Safety Performance
Reviewing findings provides key data to assess improvements in health and safety.
Followup audits can compare conditions before and after corrective actions.
Tracking progress helps organizations understand the effectiveness of their safety initiatives and make further improvements.
8. Reduces Financial and Reputational Risks
Addressing audit findings prevents costly incidents and reputational damage.
Poor chemical handling could lead to spills, injuries, or regulatory fines.
Proactive reviews minimize risks, reducing compensation claims, legal penalties, and negative publicity.
Q.1
---
1. Independent Internal Auditing
The audit was conducted independently by auditors from different departments.
Worker A was trained as an auditor and accompanied the HSM to ensure neutrality.
This approach helps eliminate bias and ensures a more objective evaluation of safety performance.
---
2. Use of a Structured Audit Procedure
The audit followed the organization's written audit procedure.
Worker A was introduced to the procedure before the audit, ensuring a systematic approach.
Following a structured procedure ensures consistency in identifying and addressing health and safety concerns.
---
3. Pre-Audit Communication with the Production Manager
The HSM informed the Production Manager (PM) in advance.
An email was sent to the PM suggesting dates for the audit.
Informing management in advance allows them to prepare for the audit, ensuring cooperation and availability of necessary documents.
---
4. Direct Observation of Work Activities
The audit involved direct observation of production processes.
The HSM and Worker A observed raw material delivery, mixing, and product transfer.
Observing real-time operations helps identify hazards that might not be documented in risk assessments.
---
5. Review of Safety Documentation
The audit included a review of key health and safety documents.
Risk assessments, accident records, and policies were examined.
Reviewing documents helps verify compliance and identify outdated or missing records.
---
6. Identification of Outdated Documents
The audit uncovered outdated health and safety documentation.
The risk assessments and health and safety policy were three years old.
Identifying outdated policies highlights the need for regular reviews to ensure they reflect current risks and best practices.
---
7. Identification of Good Practices
The audit recognized areas where the department followed safety procedures.
Workers were wearing the correct PPE as per the risk assessment.
Acknowledging good practices encourages continued compliance and motivates workers to maintain safety standards.
---
8. Classification of Findings for Clear Reporting
Audit findings were categorized into Good Practice (GP), Opportunities for Improvement (OFI), and Non-Compliance (NC).
PPE compliance was classified as GP, document retention as OFI, and chemical storage issues as NC.
Categorization makes it easier for management to prioritize corrective actions and improvements.
---
9. Raising Specific Actions for Improvement
The audit resulted in actionable recommendations.
The PM was assigned responsibility for improving chemical storage and handling within two months.
Assigning responsibilities with deadlines ensures accountability and timely corrective action.
---
10. Immediate Discussion with Workers
The HSM engaged directly with workers to gather feedback.
Worker C reported dermatitis, work fatigue, and poor housekeeping issues.
Worker engagement provides first-hand insight into workplace challenges and helps shape practical solutions.
---
11. Reporting Findings to Senior Management
The audit report was shared with the senior management team.
The PM thanked the HSM for identifying chemical storage and handling issues.
Communicating findings at a higher level ensures that necessary resources and actions are approved.
---
12. Leading to a Positive Change Management Process
The audit influenced a major safety improvement project.
The organization switched to bulk storage and transfer of raw materials, reducing manual handling risks.
A well-conducted audit can drive long-term safety improvements, enhancing both efficiency and worker well-being.
---
1. Independent Internal Auditing
The audit was conducted independently by auditors from different departments.
Worker A was trained as an auditor and accompanied the HSM to ensure neutrality.
This approach helps eliminate bias and ensures a more objective evaluation of safety performance.
---
2. Use of a Structured Audit Procedure
The audit followed the organization's written audit procedure.
Worker A was introduced to the procedure before the audit, ensuring a systematic approach.
Following a structured procedure ensures consistency in identifying and addressing health and safety concerns.
---
3. Pre-Audit Communication with the Production Manager
The HSM informed the Production Manager (PM) in advance.
An email was sent to the PM suggesting dates for the audit.
Informing management in advance allows them to prepare for the audit, ensuring cooperation and availability of necessary documents.
---
4. Direct Observation of Work Activities
The audit involved direct observation of production processes.
The HSM and Worker A observed raw material delivery, mixing, and product transfer.
Observing real-time operations helps identify hazards that might not be documented in risk assessments.
---
5. Review of Safety Documentation
The audit included a review of key health and safety documents.
Risk assessments, accident records, and policies were examined.
Reviewing documents helps verify compliance and identify outdated or missing records.
---
6. Identification of Outdated Documents
The audit uncovered outdated health and safety documentation.
The risk assessments and health and safety policy were three years old.
Identifying outdated policies highlights the need for regular reviews to ensure they reflect current risks and best practices.
---
7. Identification of Good Practices
The audit recognized areas where the department followed safety procedures.
Workers were wearing the correct PPE as per the risk assessment.
Acknowledging good practices encourages continued compliance and motivates workers to maintain safety standards.
---
8. Classification of Findings for Clear Reporting
Audit findings were categorized into Good Practice (GP), Opportunities for Improvement (OFI), and Non-Compliance (NC).
PPE compliance was classified as GP, document retention as OFI, and chemical storage issues as NC.
Categorization makes it easier for management to prioritize corrective actions and improvements.
---
9. Raising Specific Actions for Improvement
The audit resulted in actionable recommendations.
The PM was assigned responsibility for improving chemical storage and handling within two months.
Assigning responsibilities with deadlines ensures accountability and timely corrective action.
---
10. Immediate Discussion with Workers
The HSM engaged directly with workers to gather feedback.
Worker C reported dermatitis, work fatigue, and poor housekeeping issues.
Worker engagement provides first-hand insight into workplace challenges and helps shape practical solutions.
---
11. Reporting Findings to Senior Management
The audit report was shared with the senior management team.
The PM thanked the HSM for identifying chemical storage and handling issues.
Communicating findings at a higher level ensures that necessary resources and actions are approved.
---
12. Leading to a Positive Change Management Process
The audit influenced a major safety improvement project.
The organization switched to bulk storage and transfer of raw materials, reducing manual handling risks.
A well-conducted audit can drive long-term safety improvements, enhancing both efficiency and worker well-being.